How much light pressure[1] is there in the playful trail of a comet?
How much turbulence[2] is responsible for the roaring sonic boom when the plane takes off?
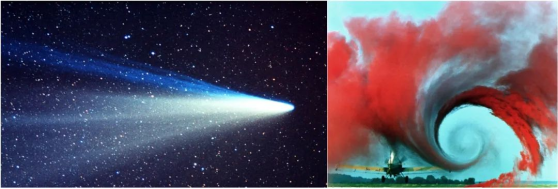
Interesting physical phenomena caused by complex stress fields - comet trail and complex airflow (source: sina)
Force is an important reference quantity in explaining physical phenomena.
Let's open our eyes wide and enter the microscopic world with curiosity about physics.
Recently, the Min Qiu’s team in Westlake University, which focuses on micro-nano technology, achieved a detection accuracy of picocoulomb using "light".
On November 21, 2023, Beijing time, the international journal Advanced Materials published online the latest research results of the cooperation between Westlake University and Hangzhou Institute of Advanced Research of the Chinese Academy of Sciences, which achieved the static micro-force sensing of picocraft based on optical waveguide. Shang Xinggang, a doctoral student of 2019 in the Nanophotonics and Instrument Technology Laboratory of Westlake University, is the first author, and Wang Ning, an associate researcher of Hangzhou Institute of Advanced Research of the Chinese Academy of Sciences (formerly a postdoctoral fellow of Professor Qiu Min's research group), Zhou Nanjia, a distinguished researcher of Westlake University, and Qiu Min, a professor of Westlake University, are the co-corresponding authors. This work has received support and funding from the National Natural Science Foundation of China, Westlake University, and Hangzhou Institute of Advanced Research of the Chinese Academy of Sciences.
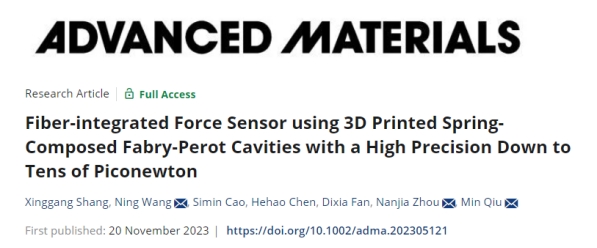
Screenshots of the paper
01 Change your mindset - think about how the vegetable market weighs?
Traditional mechanical instruments such as microelectromechanical systems, atomic force microscopes, and nanoindenters are usually developed for specific purposes, with high prices and complex use, and cannot be integrated with flexible, wearable, and other scenarios. Therefore, the development of low-cost, easy-to-use, and versatile microsensors is of great significance.
"It would be great if measuring small forces could be as simple as weighing groceries when shopping." Their research originated from a rather "down-to-earth" idea.
“Wait! Can we make a spring scale with the best performance in micro-nano scale? When I was a child, the vegetable market used spring scales for weighing. They are simple, convenient, durable, and cheap. “ Team members Wang Ning, associate researcher, Shang Xinggang, doctoral student, and Professor Qiu Min completed the foundation of the article's idea in discussions, naturally transitioning from macroscopic springs to micro-nano springs.
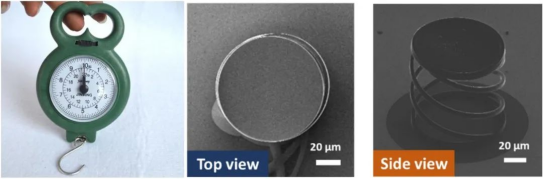
Macro (source: sina) and micro spring scale[3]
However, realizing 3D structural micro-nano springs is a great challenge. To achieve better detection limits, the requirements for the geometric parameters of the springs are extremely demanding, and common processing techniques cannot guarantee the stability of the structure. In order to achieve high-performance sensor devices, Shang Xinggang, under the guidance of Professor Qiu Min and Professor Zhou Nanjia, adopted a 3D printing method called Two Photon Polymerizations (TPP) to prepare the spring structure. He spent a full year and a half optimizing the processing techniques alone.
"Fortunately, the results are good, and the time spent is worthwhile. We have really made the most sensitive spring in the micro-nano scale, which is four orders of magnitude higher than the reported results," Shang Xinggang said.
02 Use "light" as a tool to perceive the world
After selecting 3D micro-nano springs as the key mechanical component, the next key issue is how to accurately measure the small deformation of the springs after being stressed.
" light! How about trying optical fiber?"
In the eyes of Qiu Min's team, light can not only illuminate the world, but also be regarded as an important tool for sensing the world. In addition, as a special substrate, optical fiber has outstanding advantages in micro-nano sensing and imaging, such as flexibility, all-optical modulation, and resistance to electromagnetic interference. Based on the previous explorations of Dr. Cao Simin and Shang Xinggang[4-5], the team realized the preparation of micro-springs across the "substrate" from flat glass to optical fiber end faces.
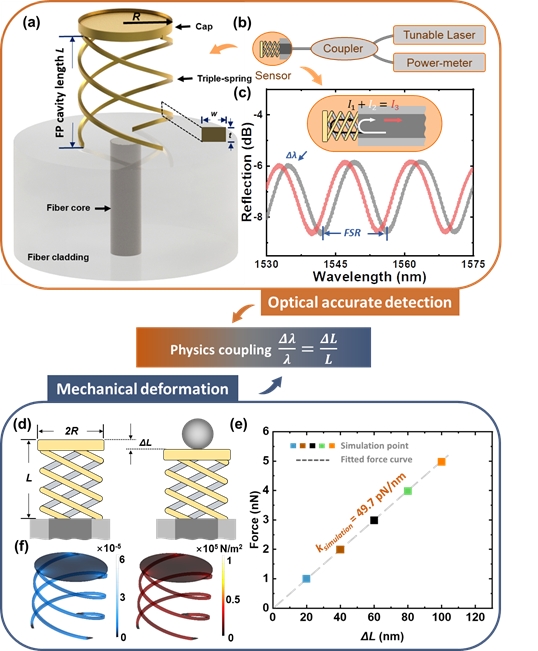
Principle of Spring Fiber Optic Micro Force Sensor[3]
By preparing a spring on the end face of an optical fiber, a Fabry-Perot (FP) interferometric cavity is naturally formed, and the position of the spectral valley is closely related to the cavity length. Experimentally, by analyzing the spectral shift and using the intermediate value of the structural compression, the structural stress can be obtained.
Coupled with a high-precision spectrometer, the sensitivity and detection limit of the spring-based fiber optic sensor are 0.436 nm/nN and 40.0 pN, respectively.
03 Meaning of “40 picograms”
The mass of a one-centimeter hair is 0.1 milligram, which is approximately 1 micro-newton (μN). '40 picograms' is only one-ten-thousandth of the weight of a hair. If you really want to find a visual measurement, 40 picograms is approximately one-tenth the weight of a red blood cell.
Most common mechanical sensors can only achieve sub-micro to nano-newton accuracy, and cannot accurately detect subtle physical processes such as cell mass detection (~pN), photonic force (~100 pN), air flow force (~nN), etc. In addition, insufficient data accuracy can mask nonlinear physical processes, leading to erroneous interpretation of phenomena. Therefore, improving sensor accuracy can greatly enhance device reliability and expand its application range.
The performance of the Pioneer-class fiber optic sensor is comparable to that of MEMS sensors, and is expected to make up for the deficiencies of instruments such as MEMS, AFM, and nanoindentation instruments in the areas of strong electromagnetic interference, flexibility, and wearability.
Comparison chart of the performance of various types of sensors[3]
04"Capture" non-linear airflow pressure
The sensor is applied to the detection of minute air flow forces at the micrometer scale. Thanks to the accuracy of the picocoulomb level, the non-linear trend of air flow forces with pressure was detected in the experiment. During the cyclic change of pressure, the consistency of the measured spectra under the same pressure was good, and the spectral valley positions were almost the same, demonstrating the excellent stability and repeatability of the sensor.
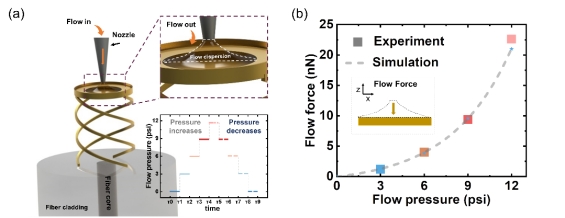
Air flow force sensing[3]
Confused by the experimental phenomenon of nonlinear airflow force, Xinggang Shang consulted another PI of the School of Engineering, Professor Fan Dixia, an expert in fluid mechanics. Under the guidance of Fan Dixia, Shang Xinggang obtained computational simulation results that revealed the nonlinear variation trend of airflow force stemmed from different dispersion levels of airflow. The flow direction of high-pressure airflow was more concentrated in the axial direction of the sensor, resulting in a rapid increase in airflow force.
05 What else can the "Leather Cow Spring Scale" do?
In the micro-world of the "vegetable market", there are also a large number of "cucumbers, tomatoes, potatoes" waiting for the micro-spring scale to show its skills.
"Perhaps one day in the future, we can accurately measure the dry weight of cells," Shang Xinggang dreamed.
Through further design, the sensor is also expected to be used for accurate detection of turbulence. In addition, thanks to the flexibility of optical fibers, the system can provide new ideas for in-situ blood pressure detection, respiratory monitoring, and other important application scenarios.
bibliography
[1] https://m.thepaper.cn/baijiahao_11711587
[2] https://www.thepaper.cn/newsDetail_forward_1753895
[3] https://onlinelibrary.wiley.com/doi/10.1002/adma.202305121
[4] Two-photon direct laser writing of micro Fabry-Perot cavity on single-mode fiber for refractive index sensing. Optics Express, 2022, 30 (14): 25536-25543.
[5] PDMS-filled micro-spring Fabry-Perot cavity for temperature sensing. Optics Express, 2023, 31 (19): 30332-30339.
Paper Linking:https://onlinelibrary.wiley.com/doi/10.1002/adma.202305121
Reprinted from: School of Engineering, Westlake University official account